Мелкосерийное литье пластика подразумевает производство изделий из полимерного сырья в небольших объемах – в пределах нескольких сотен или тысяч единиц. Такие технологии позволяют получать отливки разной сложности с хорошей детализацией и высоким уровнем точности, причем быстро и с минимальными вложениями. В зависимости от используемой полимерной массы, изготавливаемые детали могут быть эластичными, жесткими, термостойкими, разных цветов и степени прозрачности.
Преимущества технологии
При мелкосерийном литье полимерных изделий достигаются:
- Гибкость – возможность изменения дизайна и параметров деталей, в т. ч. при разработке прототипов и адаптации продуктов под цели заказчика.
- Индивидуальность – возможность изготовления уникальных деталей любой геометрии.
- Эффективные вложения, доступные для небольших предприятий – т.к. при изготовлении небольших партий не нужно создавать сложные пресс-формы и инвестировать крупные суммы в покупку высокопроизводительного оборудования (в отличие от массового производства). Производить небольшие партии изделий можно на настольной литьевой машине с помощью полимерных пресс-форм, созданных на 3D-принтере. В отличие от металлических пресс-форм, которые дорогие и изготавливаются 1–2 месяца, полимерные литформы более доступны. Тем не менее, они позволяют производить ограниченными тиражами высококачественные, воспроизводимые изделия.
- Быстрая разработка, короткие сроки производства, возможность реализации инновационных идей и оперативного вывода готового продукта на рынок.
- Возможность использования разных типов термопластиков – ABS, PA, PE, PS, PP, PC, POM, ASA, TPE, TPU и др.
- Четкое воспроизведение, высокое качество и точность получаемых отливок.
Когда и для чего используют литье пластика малыми партиями?
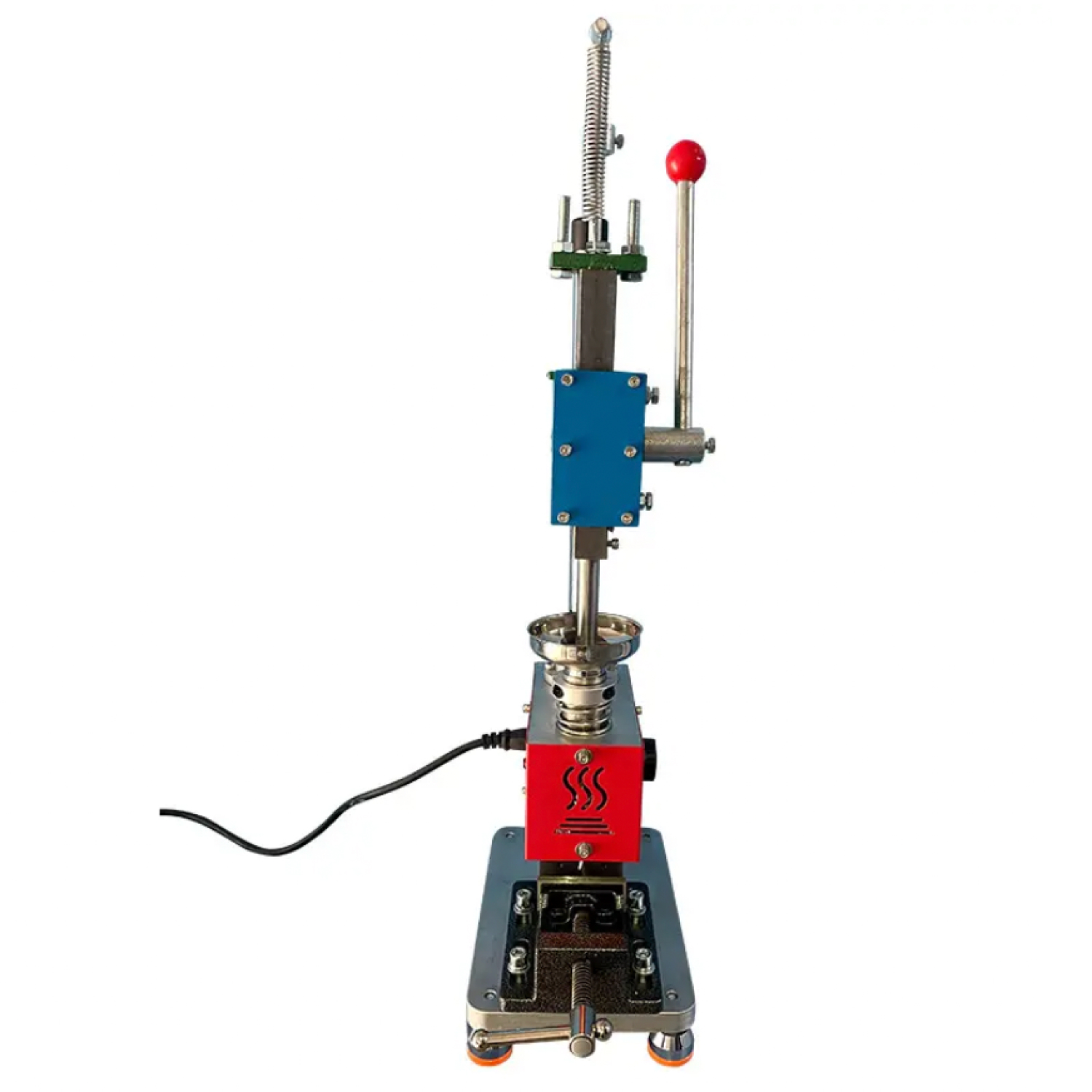
Пластиковые детали, изготавливаемые малыми партиями при помощи литья под давлением, востребованы в разных сферах. В частности, так производят компоненты медтехники, автомобилей, электроники и бытовой техники, игрушки и сувениры, прототипы и лимитированные серии изделий.
Из-за большой стоимости оборудования и износостойких пресс-форм литье пластмасс под давлением преимущественно используют на предприятиях для серийного производства. Но термопластавтоматы вертикального типа сделали эту технологию доступной для небольших производственных компаний и рентабельной для изготовления небольших партий изделий, в т. ч. на заказ. Поэтому они отлично подходят для краткосрочного литья, проектирования прототипов, выпуска пилотных партий, создания нестандартных и мелкосерийных моделей.
Виды мелкосерийного литья пластмасс
Для изготовления мелких партий полимерных изделий используют разные технологии:
- Инжекционное прессование или литье под давлением на вертикальных литьевых машинах (термопластавтоматах, ТПА)– самый распространенный и эффективный метод для мелкосерийного изготовления полимерных деталей. Позволяет производить прочные изделия с точным соблюдением размеров. Разогретый пластик под давлением впрыскивается в литформу, где остывает и приобретает заданную ее геометрией конфигурацию. По окончании цикла пресс-форма размыкается, отливки выталкиваются, и производственный цикл повторяется.
- 3D-печать – распространенная технология для немассового литья пластмасс. На 3D-принтерах удается печатать изделия сложной геометрии и даже комбинировать материалы.
- Вакуумное формование – позволяет изготавливать плоские или немного изогнутые детали, в т. ч. крупные. Полимерное сырье нагревается и при помощи вакуума вытягивается в форму.
- Реактивное литье – применяется для изготовления сверхпрочных деталей, стойких к химическим воздействиям. В отличие от литья термопластичных пластмасс при инжекционном прессовании, при реактивном литье в качестве сырья используют термореактивные смеси пластика и твердителя.
Особенности полимерных пресс-форм, изготовленных на 3D-принтере
Пресс-формы для немассового литья полимеров все чаще делают на 3D-принтерах. В среднем ресурс полимерных литейных форм составляет до 500 циклов и вполне устраивает при литье небольших партий, в частности, при необходимости быстрого изготовления прототипов или нестандартных деталей. Такие пресс-формы подходят как для настольных ТПА, так и для промышленных литьевых машин.
Это позволяет изготавливать серии деталей из термопластиков за пару дней. Более того, на 3D-принтерах можно печатать формы, которые проблематично изготовить классическим методом. При помощи стереолитографической 3D-печати создают пресс-формы с гладкой поверхностью, которые обеспечивают хорошую точность литья и легкое извлечение деталей.
Конечно, по производительности и рабочему ресурсу литформы из полимера уступают металлической оснастке. В полимерной форме теплопередача и охлаждение происходят медленнее, и сложнее обеспечить строгие допуски по размерам. По прочности пластик уступает металлу, но даже под действием высоких температур и давления полимерные формы выдерживают сотни производственных циклов.
Алгоритм производственного процесса
Литье мелких партий изделий из термопластичных полимеров включает следующие этапы:
- Проектирование литформы в любой программе САПР.
- Выбор полимерного материала (с хорошими показателями прочности, жесткости и термостойкости, например, Rigid 10K Resin с высотой слоя 50 микрон) и изготовление литформы на 3D-принтере.
- Промывка, финишная полимеризация, шлифовка и сборка литформы. Для увеличения ресурса желательно поместить ее в каркас или формовочный блок из металла.
- Установка литформы в термопластавтомат, выполнение настроек и заправка приемочного блока пластиковыми гранулами. Проще в обработке пластмассы, нагреваемые до 250 °С (TPE, PP, PE), и пресс-формы при работе с таким сырьем служат дольше.
- Тестирование производственного процесса и выбор оптимальных рабочих параметров.
- Охлаждение отливок и их извлечение из литформы.
Читайте в предыдущей статье блога Shura-Master.ru о том, что такое мотор-колесо, из чего оно состоит и как работает.